Defects In Sheet Metal Drawing
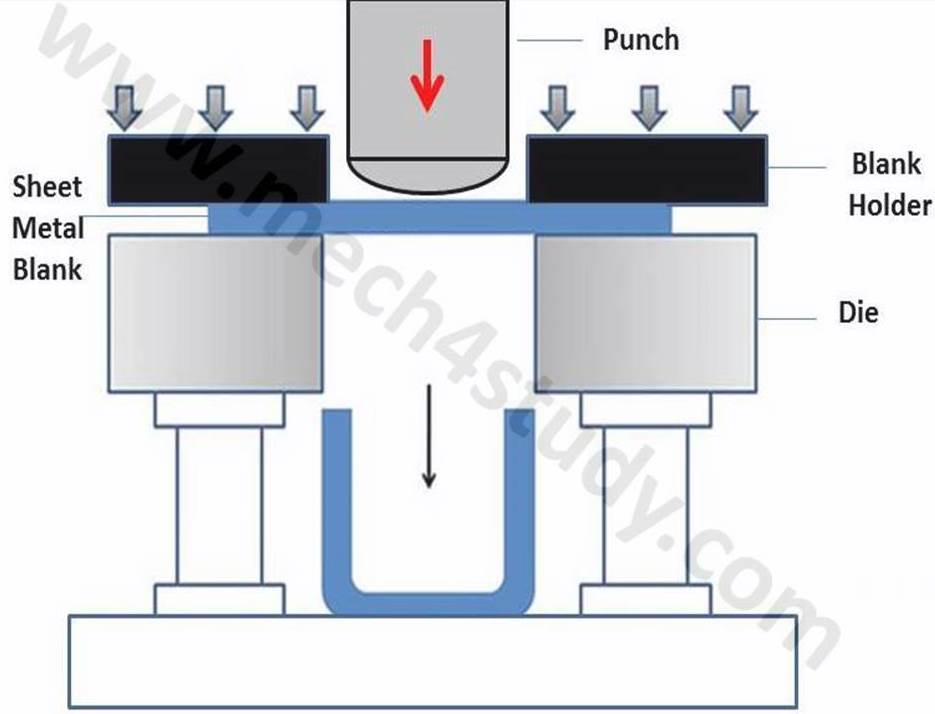
Predict part defects tearing wrinkling dimensional inaccuracy and propose.
Defects in sheet metal drawing. Excessive thinning thickening of the sheet during forming. The proper relation of views in a drawing. During this process the blank sheet will develop defects if the process parameters are not selected properly. Springback or final part deviation from nominal incorrect process or number of forming tools.
Stamping auto body panels 3 to 5 dies each prototype dies 50 000. There are two reasons behind this defect. Excessive thinning in areas of the sheet metal is also an unwanted defect. One is the improper handling another one is the elasticity of sheet metal forming materials.
Causes of these are mostly too high or improper force distribution and material considerations. How to dimension a drawing. The reason behind it is that welding positions are misaligned. Accuracy in the use of the scale rule.
As its name indicates the formation of ears at the free edges of a deep drawn cylindrical cup is known as earing defect fig. This defect is caused by the anisotropy of the sheet metal. Tearing is one of the most common defects. Sheet metal stamping drawing car industry 90million cars and commercial vehicles produced worldwide in 2014.
Causes of these are mostly too high or improper force distribution and material considerations. Failure of sheet metal parts during deep drawing processes usually takes place in the form of wrinkling or tearing. Defects that occur during deep drawing of sheet metal can be controlled by careful regulation of process factors. In making the layout for this cleat the following points must be kept in mind.
Tearing is one of the most common defects. The sheet metal cleat the work of this problem will consist in laying out to full size the views and pattern for a galvanized sheet metal cleat. The main reasons for the cracking are over stretching or stress concentration. Wrinkles splits and springback are the three most common defects encountered during sheet metal stamping.
Defects that occur during deep drawing of sheet metal can be controlled by careful regulation of process factors. One of the primary defects that occurs in deep drawing operations is the wrinkling of sheet metal material generally in the wall or flange of the part. Figure a wrinkling in the flange or b in the wall c tearing d earing e surface scratches basic press working operation sheet metal working is also a metal forming operation where the material being worked is in the form of sheets the working is usually at room temperature. The flange of the blank undergoes radial drawing stress and tangential compressive stress during the stamping process which sometimes results in wrinkles.